While companies like Isnnova and Lonati SpA have 3D printed valves for ventilators, others firms like RapidMade are now producing emergency personal protective equipment (PPE) such as lightweight plastic face masks with built-in removable filters as well as face shields. Groups like the Covid Maker Response (CMR) are also manufacturing, assembling and distributing 3D-printed PPE to health care workers on the front lines. CMR was founded by members of Columbia University Libraries, Tangible Creative and MakerBot.
Cloud-based 3D printing software has further given manufacturers the ability to easily make any part on demand, boosting the cause of additive manufacturing.
3D printing, however, is not just about plastic, although the story of 3D printing did begin in the 1980s with plastic, which remains the most widely used material. This is not surprising since plastic is readily available, comparatively inexpensive and well established in a variety of extrusion processes.
That said, 3D printers today also use metals, alloys and composites. These materials are being used not only to make PPE and other medical equipment, but also jewelry and toothbrushes, football boots, racing-car parts, machine parts, custom-designed cakes, human organs, houses and airplane parts, among countless other items.
Metals and alloys such as aluminum, steel, stainless steel, gallium, titanium and cobalt-chromium are widely used in the aeronautics, automotive and biomedical industries, and use processes such as selective laser sintering (SLS), direct metal laser sintering (DMLS) or e-beam (EBM). 3D printers also use materials such as ceramics, sand, organic materials, marble, stone, and wood, depending on the applications.
The Power of Composites
Composite and metal 3D-printed parts fulfil different roles on the factory floor and can complement each other to support production.
Using both a metal and a composite printer provides the flexibility to leverage the strengths of both materials and create extremely functional tools [MG1] .
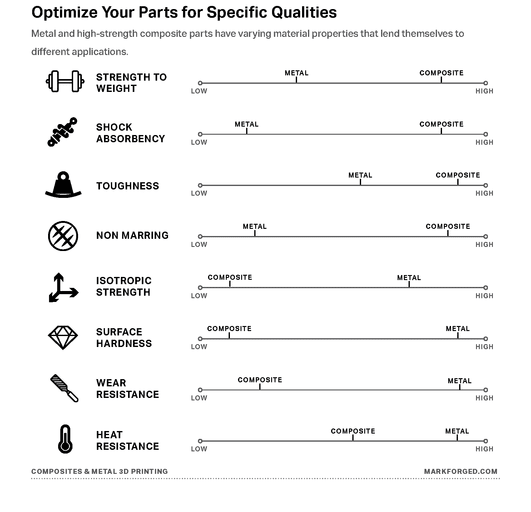
Composites, which are now getting their due in the field of 3D printing, can be broadly defined as materials that contain a reinforcement (such as fibers or particles) supported by a binder (matrix) material. The matrix provides a medium for binding and holding reinforcements together in a solid. Most composites offer significantly high advantages in terms of their specific strength (strength-to-weight ratio) and specific stiffness (stiffness-to-weight ratio).
Composites can be broadly classified according to reinforcement forms—particulate reinforced, fiber reinforced, or laminar composites.
Fiber-reinforced composites can be further divided as those containing discontinuous or continuous fibers. Fiber-reinforced composites, which contain reinforcements having lengths much greater than their cross-sectional dimensions, are considered to be discontinuous or short fibers if their properties vary by fiber length. Otherwise, these composites are considered to be continuous fiber reinforced [MG2] .
The percentage of fiber used and the base thermoplastic determine how strong the final part is. In the case of continuous fiber, long strands of fiber are mixed with a thermoplastic, like PLA, ABS, nylon, PETG and PEEK during the printing process. Parts that are 3D printed with continuous fiber are extremely lightweight yet as strong as metal.
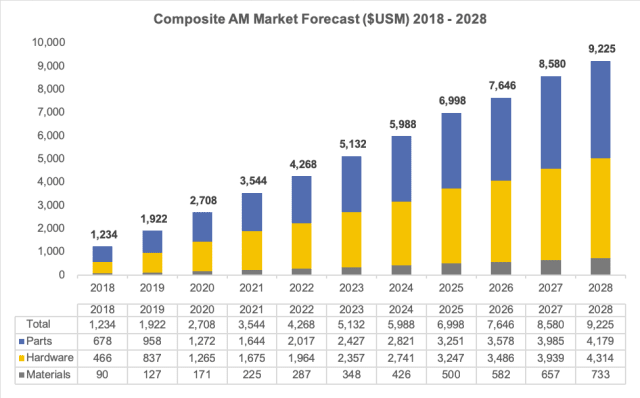
Why Single out Carbon Fiber?
Most 3D printers capable of processing composite materials are based on the polymer-extrusion process, known as fused filament fabrication (FFF). In FFF, a nozzle moves above the build platform, extrudes a melted thread of plastic called a filament, and creates an object layer-by-layer.
Carbon fiber is one of the most popular types of fibers used in 3D printing, followed by fiberglass and Kevlar. If you need a strong yet light 3D-printed machinery part, you may want to consider carbon fiber. It’s a solid material that is incredibly strong—five times stronger than steel—yet significantly lighter in weight.
Hence, carbon fibers find applications in aerospace, road and marine transport, sporting goods, audio equipment, loudspeakers for hi-fi equipment, pickup arms, robot arms, automobile hoods, novel tooling, casings surgery and X-ray equipment, implants, valves, seals, and pump components in process plants, and radiological equipment, among others.
Composition
Carbon fibers are mostly made from polyacrylonitrile (90 percent), with the remaining 10 percent made from rayon or petroleum pitch—all organic polymers formed by a long string of molecules bound together by carbon molecules.
The raw material used to make carbon fiber is called the precursor . It is drawn into long strands heated to a very high temperature without allowing them to come in contact with oxygen so that the fiber cannot burn. The process called carbonization creates long, tightly woven fibers that are coated to protect them from damage during winding or weaving.
The 3D printing of filaments containing chopped fibers requires only a hardened steel nozzle to resist abrasive fiber strands. The FFF process for continuous fiber printing, however, requires a second nozzle to separately deposit a single, uninterrupted strand of fiber.
Pros and Cons
Carbon fiber has many positive qualities. It has a high specific strength, or strength-to-weight ratio. It is highly rigid, corrosion resistant, and chemically stable. It has good tensile strength—the maximum stress that a material can withstand while being stretched or pulled before necking, or failing.
Carbon fiber is fire resistant and has a low coefficient of thermal expansion—a measure of how much a material expands and contracts when the temperature increases or decreases. Carbon fiber is also nonpoisonous, biologically inert and X-ray permeable—qualities that make it beneficial in medical applications.
However, carbon fiber is also electrically conductive, which can be both helpful and troublesome. In addition, it is relatively expensive. Further, carbon fibers are brittle—its layers are formed by strong covalent bonds, which allow for cracks at very low strain.
Chopped Carbon Fiber
In this method, the carbon fiber is already integrated into the filament and is ready to print on an FFF 3D printer (right nozzle and heated bed). A base material (PLA, nylon, or other thermoplastics) is mixed with extremely small bits of carbon fiber. These small carbon fiber strands are abrasive, so the 3D printer will require a hardened steel nozzle or other tough nozzle to resist them.
Parts printed with this type of filament are stronger than regular thermoplastic prints, but the percentage of fiber used and the base thermoplastic (among other variables) determine the strength of the final product.
Consider the case of vehicle drive systems made of components that deliver power to the driving wheels, and which require complex under-the-hood assemblies that are configured using a complex series of tools and jigs that are fully customized for builds. Rather than use CNCs to machine gauges, electric vehicles solution provider Dayco 3D printed them in Onyx (from Markforged). The 3D-printed material is a low cost, high strength thermoplastic made up of nylon and chopped carbon fiber.
3D printing helped Dayco automate the production of these parts, freeing up skilled CNC machining labor to focus on manufacturing high-value production processes. Dayco, according to Markforged, also saved 70 percent in costs and halved its overall production time from 200 to 100 hours.
Another case in point is that of Utah Trikes—a producer of trikes, quads and custom wheelchairs—which needed the ability to make prototype pieces it could actually test, and which would be both cost- and time-efficient. A pedal-powered wheelchair in production at Utah Trikes has 450 distinct parts, 120 of which are 3D printed.
The company used the Stratasys FDM Nylon 12CF, which has given Utah Trikes the “... ability to now design and print on-site, which has cut production time from two months to two weeks, reducing the company’s costs 8-10 times,” according to the Stratasys website.
Other filament manufacturers of short fiber composites include Roboze, 3DXTech, Proto-Pasta and colorFabb.
The future Bets on Continuous Carbon Fiber
Companies that use the continuous 3D printing method include Markforged, Anisoprint, CEAD, Roboze, EnvisionTEC and Impossible Objects. Continuous carbon fiber 3D printers typically range between $14,000 and $250,000, depending on the size and applications.
The continuous fiber method was first introduced by Markforged in 2014, when the company launched the Mark One. While the Mark One has been replaced by a new generation of 3D printers, the technology hasn’t changed. Typically, the printer is equipped with two nozzles—one to extrude the plastic filament and the other to simultaneously lay down carbon fiber strands.
The technology goes by different names with a few variations. While Markforged calls it Continuous Filament Fabrication (CFF), start-up Anisoprint has christened it Composite Fiber Co-extrusion (CFC
As an example of the practical applications of this technology [MG3] , para-athlete diver Dmitry Pavlenko needed a lever to control air inflation and release for maintaining buoyancy and manoeuvrability. He began by using a steel spoon as a lever, but it broke after the 10th dive. Another lever was printed on an Anisoprint Composer 3D printer from PETG (a glycol-modified version of polyethylene terephthalate (PET), which is commonly used to manufacture water bottles) and reinforced with composite carbon fiber in a bid to increase the life span of the part. Pavlenko believes the Anisoprint-printed part will survive 100 dives.
Silicon Valley-based AREVO’s proprietary process is based on Directed Energy Deposition (DED) technology, where a laser is used to heat the filament and carbon fiber at the same time as a roller compresses the two materials together. Its additive manufacturing process features patented software algorithms enabling generative design techniques, free-motion robotics for “true 3D” construction, and DED “for virtually void free construction all optimized for anisotropic composite materials,” according to the company.
As an example of its technology at work, AREVO produces 3D-printed carbon fiber unibody frames for a new line of e-bikes called EVE9 from the Pilot Distribution Group BV—a leader in bike design and production. “AREVO’s continuous carbon fiber technology is very impressive as it affords numerous design possibilities and provides excellent strength and durability,” said Arno Pieterse from Pilot.
According to a September 2019 press statement, Hemant Bheda, Cofounder and Chairman of AREVO, sees “near-term applicability (of this technology) in other areas of green urban mobility, from electric scooters to e-VTOLs, or flying cars.”
Impossible Objects and EnvisionTEC have added systems for continuous fiber 3D printing to their range of machines. There’s a technology twist, though, since they weave in sheets of carbon fiber into a print by using a lamination process. On its part, Continuous Composites [MG4] uses a hybrid technology where the strand of fiber is soaked with resin and then hardened using UV light, a process similar to SLA 3D printing.
Switzerland-based 9T Labs uses a 3D printing process it calls Additive Fusion Technology (AFT)—the reinforcement is made from a carbon-filled material instead of pure carbon fibers.
The method that U.S.-based Continuous Composites employs is called Continuous Fiber 3D Printing (CF3D). It feeds a roll of dry carbon fiber into a print head mounted on a seven-axis industrial robot. Inside of the print head, the fiber is impregnated with a rapid curing photopolymer resin and is then extracted through the end effector and instantly cured with a powerful energy source.
Market Opportunity
The global 3D printing market size was valued at $12 billion in 2019 and is expected to expand at a CAGR exceeding 14 percent from 2020 to 2027, according to a February 2020 note by market research firm Grand View Research Inc. The polymer (or loosely, plastics) segment accounted for the largest market share in 2019 as compared to the metal and ceramic segments. However, the metal segment is anticipated to hold the largest market share and continue leading 3D printing market share over the forecast period.
According to Stratview Research, additive manufacturing is still at a nascent stage in the composites industry. Still, the technology does possess huge opportunities in most of the industry verticals, including aerospace, defence and automotive. The global 3D printed composites market is pegged to reach $190 million in 2024, according to Stratview Research. Carbon fiber, the research firm adds, is projected to remain the largest reinforcement type in the market during the forecast period.
Market research firm IDTechEx is much more bullish. It forecasts the global market for composite 3D printing will touch $1.7 billion in value by 2030.
The high demand for lightweight components in the structural applications for improving fuel efficiency or reducing carbon emissions is expected to be the leading growth driver of the increased demand for carbon fibers in major industries such as aerospace, defense and automotive.
As is evident from the examples above, continuous carbon fiber 3D printing can produce parts that boast high strength, stiffness, and dimensional stability. These parts are light, have a great surface finish, and can be mixed with many different kinds of thermoplastic materials.
However, 3D printing parts with carbon fiber remains expensive. Costs, though, are expected to fall as companies increasingly see its utility. With rising volumes, carbon fiber 3D printing may live up to the promising forecasts.